Plasma Cutting Services Market Trends for 2025 and Best Practices for Maximizing Efficiency
The plasma cutting services market is poised for significant growth, with projections indicating an increase in demand driven by advancements in manufacturing technologies and the rising need for precision cutting applications. According to industry reports, the global plasma cutting services market is anticipated to reach approximately $X billion by 2025, reflecting a compound annual growth rate (CAGR) of Y% from 2020. This growth can be attributed to sectors such as automotive, aerospace, and construction, which increasingly rely on plasma cutting for its ability to provide high-quality finishes and efficiency in various metal cutting tasks.
As this market evolves, it becomes imperative for service providers to adopt best practices that enhance operational efficiency and reduce costs. Implementing state-of-the-art equipment and adopting innovative techniques can significantly impact productivity levels. Furthermore, a focus on skilled workforce training and effective maintenance strategies is crucial in optimizing plasma cutting services. By staying ahead of industry trends and leveraging technology, businesses can not only improve their service offerings but also capture a larger share of the expanding plasma cutting services market.
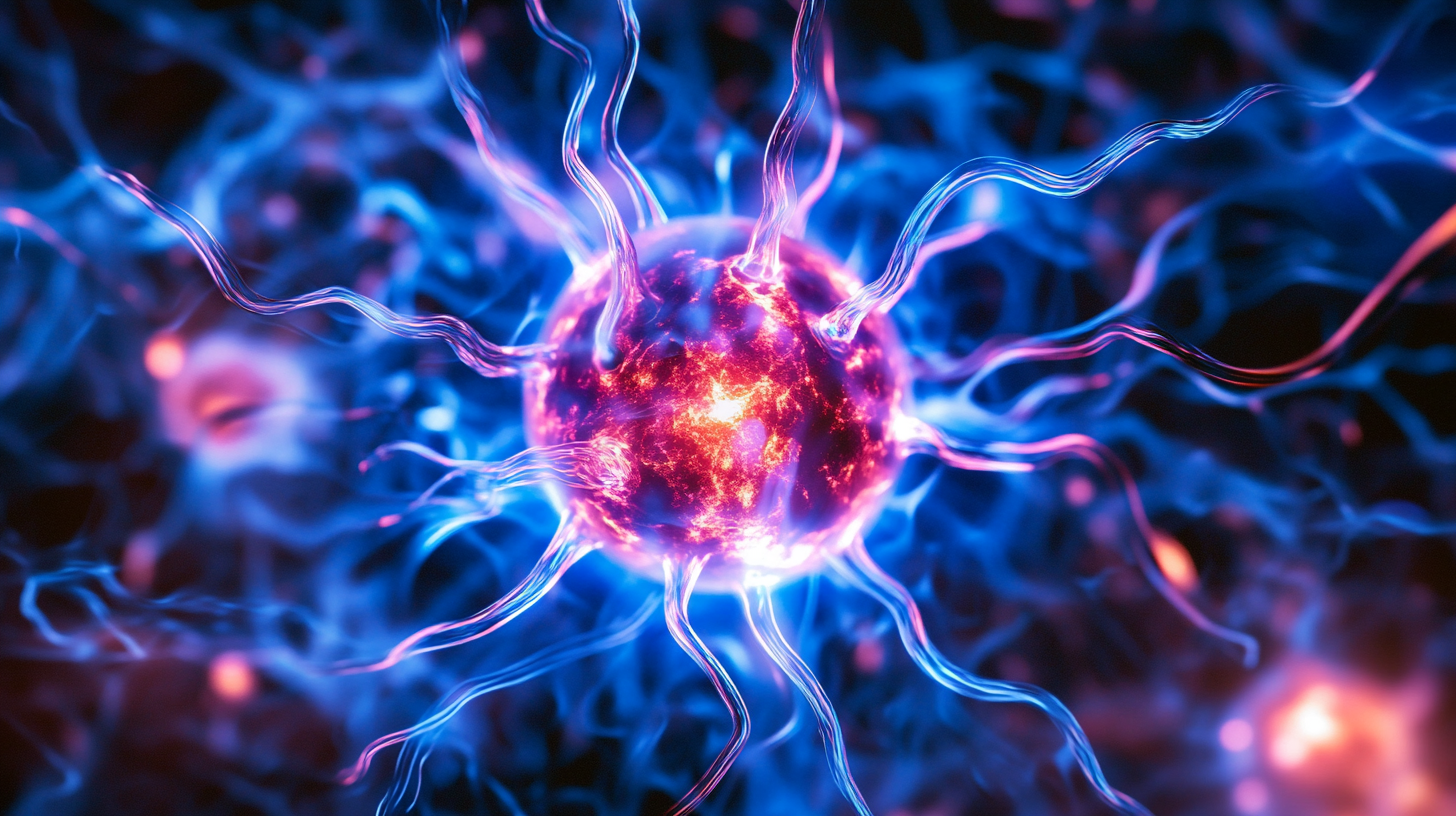
Emerging Trends in Plasma Cutting Technology for 2025
In the rapidly evolving landscape of plasma cutting technology, several emerging trends are set to shape the industry by 2025. One of the most significant advancements is the integration of automation and robotics into plasma cutting processes. These technologies not only enhance precision and consistency but also significantly reduce labor costs and increase production efficiency. As industries look for ways to streamline operations, automated plasma cutting solutions are expected to become more prevalent, making it easier to handle complex tasks with minimal human intervention. Another noteworthy trend is the focus on developing more energy-efficient plasma cutting systems. As environmental concerns continue to rise, manufacturers are prioritizing technologies that reduce energy consumption without compromising performance. Innovations in power supply design and torch technology are leading to systems that can deliver higher cutting speeds while using less electricity. This shift not only helps companies save on energy costs but also aligns with the global push towards sustainability. Additionally, advancements in software and digital tools are revolutionizing how plasma cutting services are managed. Companies are increasingly adopting smart software solutions that leverage data analytics and AI to optimize cutting parameters and improve workflow. This data-driven approach allows operators to make more informed decisions, resulting in enhanced productivity and reduced material waste. As these technologies mature, businesses that embrace them will likely find themselves at a competitive advantage in the plasma cutting market.
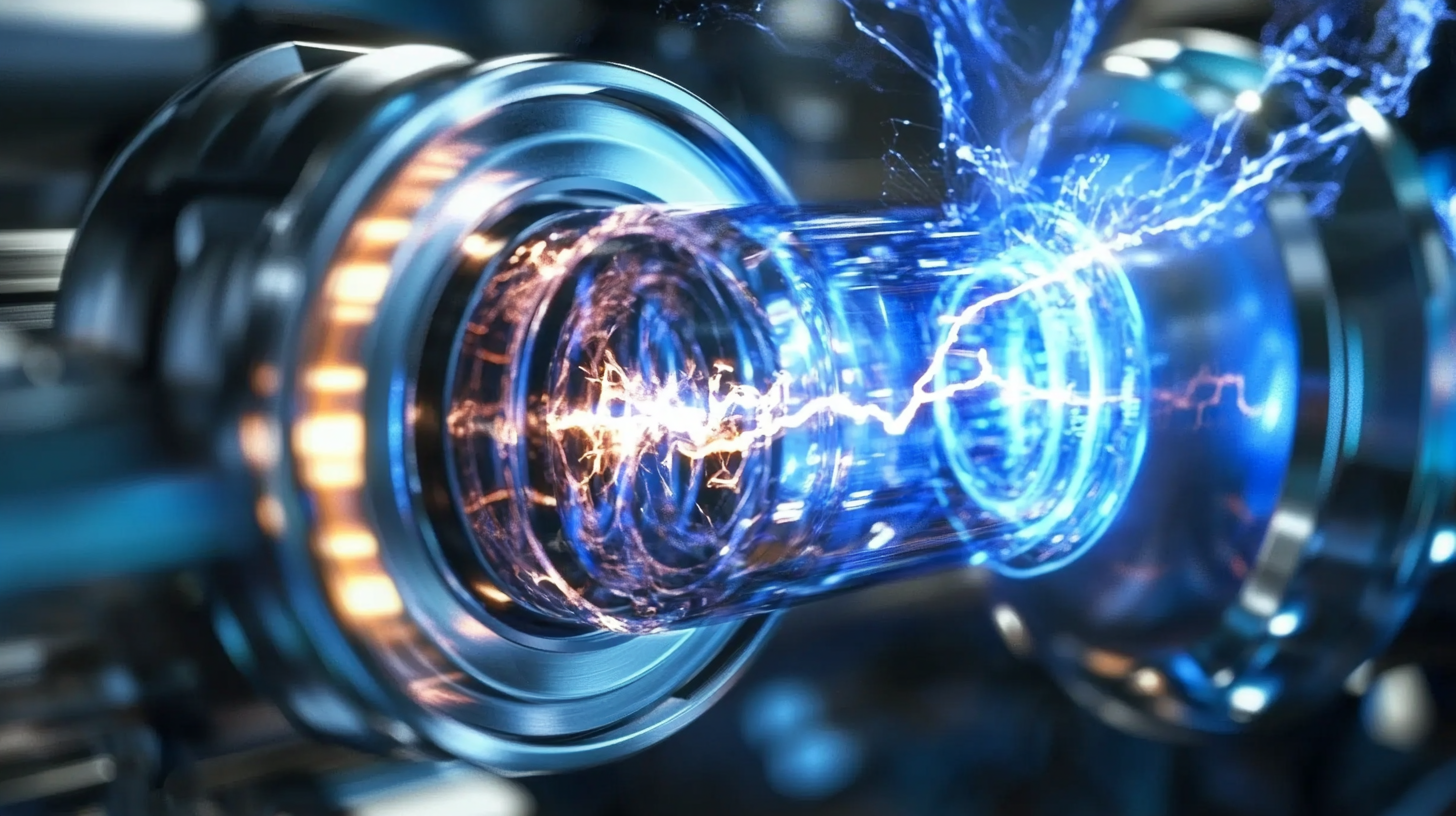
Key Factors Driving Growth in the Plasma Cutting Services Market
The plasma cutting services market is poised for significant growth through 2025, driven by various key factors that enhance operational efficiency and reduce costs. According to a report by Research and Markets, the global plasma cutting market is expected to exceed $7 billion by 2025, reflecting a compound annual growth rate (CAGR) of more than 5.5%. This growth is primarily fueled by the increased demand in the automotive and aerospace industries, where precision and speed are crucial.
One of the main drivers of growth is technological advancements. Innovations in plasma cutting systems, such as the introduction of automation and improved nozzle designs, have resulted in greater precision and faster cutting speeds, allowing businesses to increase productivity. Furthermore, companies are increasingly adopting CNC (Computer Numerical Control) plasma cutting solutions, which not only enhance accuracy but also significantly reduce material wastage.
Another critical factor is the rising demand for lightweight metals. Industries are moving towards the use of aluminum and other non-ferrous materials that require specialized cutting techniques. The Global Market Insights report emphasizes that the demand for plasma cutting processes in these sectors will continue to rise, as they enable manufacturers to efficiently handle the unique challenges posed by lighter materials. As a result, organizations that invest in advanced plasma cutting technologies are likely to gain a competitive edge in their respective markets.
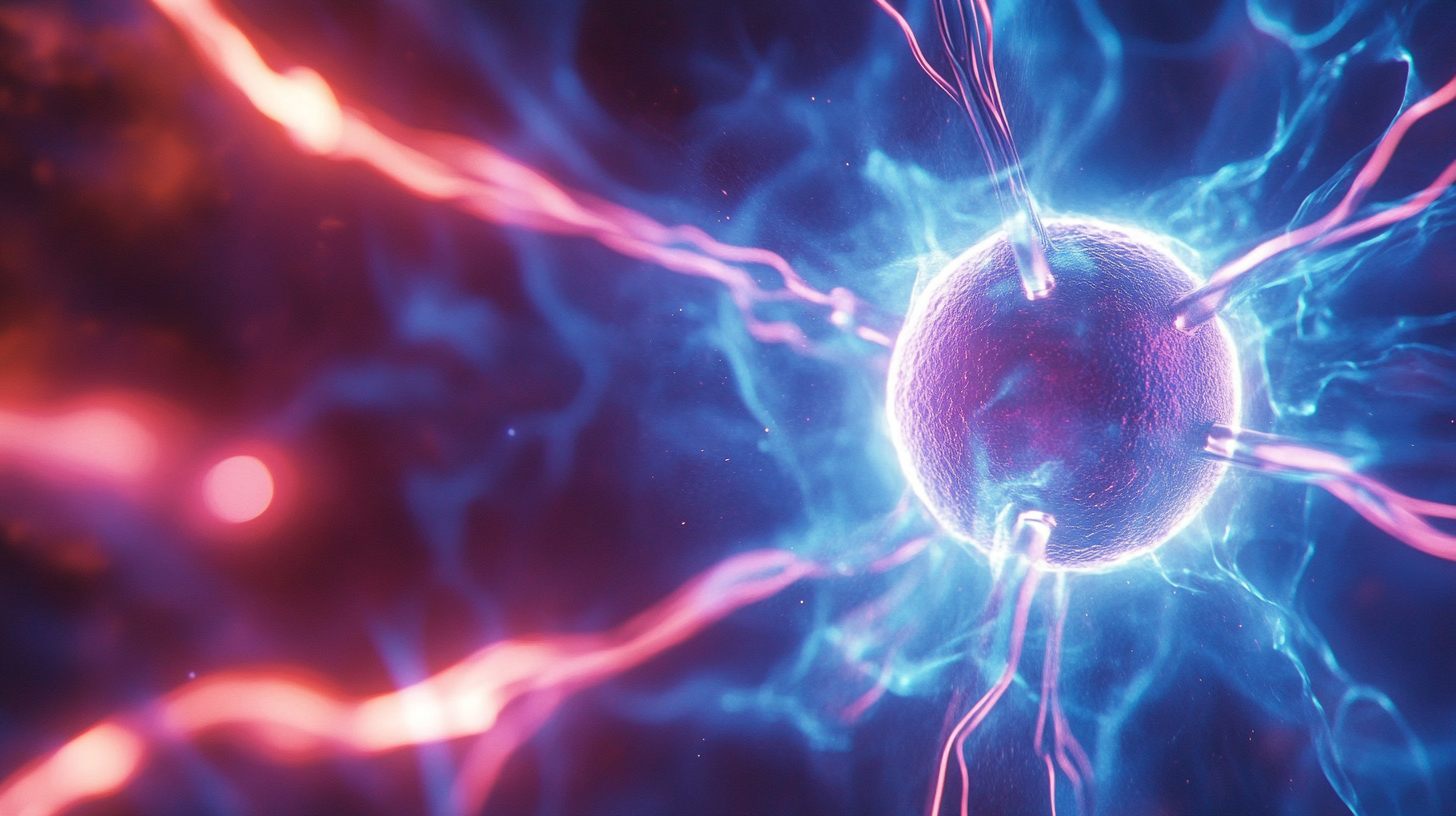
Best Practices for Enhancing Plasma Cutting Efficiency
In the competitive landscape of plasma cutting services, enhancing efficiency is paramount for maximizing productivity and reducing costs. Best practices in plasma cutting not only ensure high-quality results but also optimize resource usage and workflow. One effective strategy is the implementation of advanced nesting software, which allows fabricators to minimize material waste while maximizing output. According to industry reports, effective nesting techniques can lead to savings of up to 20% in material costs, a significant advantage in budget management for fabrication projects.
Moreover, integrating plasma technology with emerging applications, such as gas conversion, can improve operational efficiency. For instance, recent advancements in plasma-activated processes demonstrate potential in converting CO2 into useful chemicals and renewable fuels, which can lead to a more sustainable fabrication environment. By adopting such innovative technologies, businesses can enhance their production capabilities while contributing to environmental sustainability.
Additionally, ongoing training and development for technicians in the latest plasma cutting technologies will empower workers to utilize equipment to its full potential. Continuous education and skill enhancement are vital; studies show that companies investing in employee training see productivity gains of up to 30%. Implementing these practices not only streamlines operations but also ensures that fabricators remain competitive in a rapidly evolving market landscape.
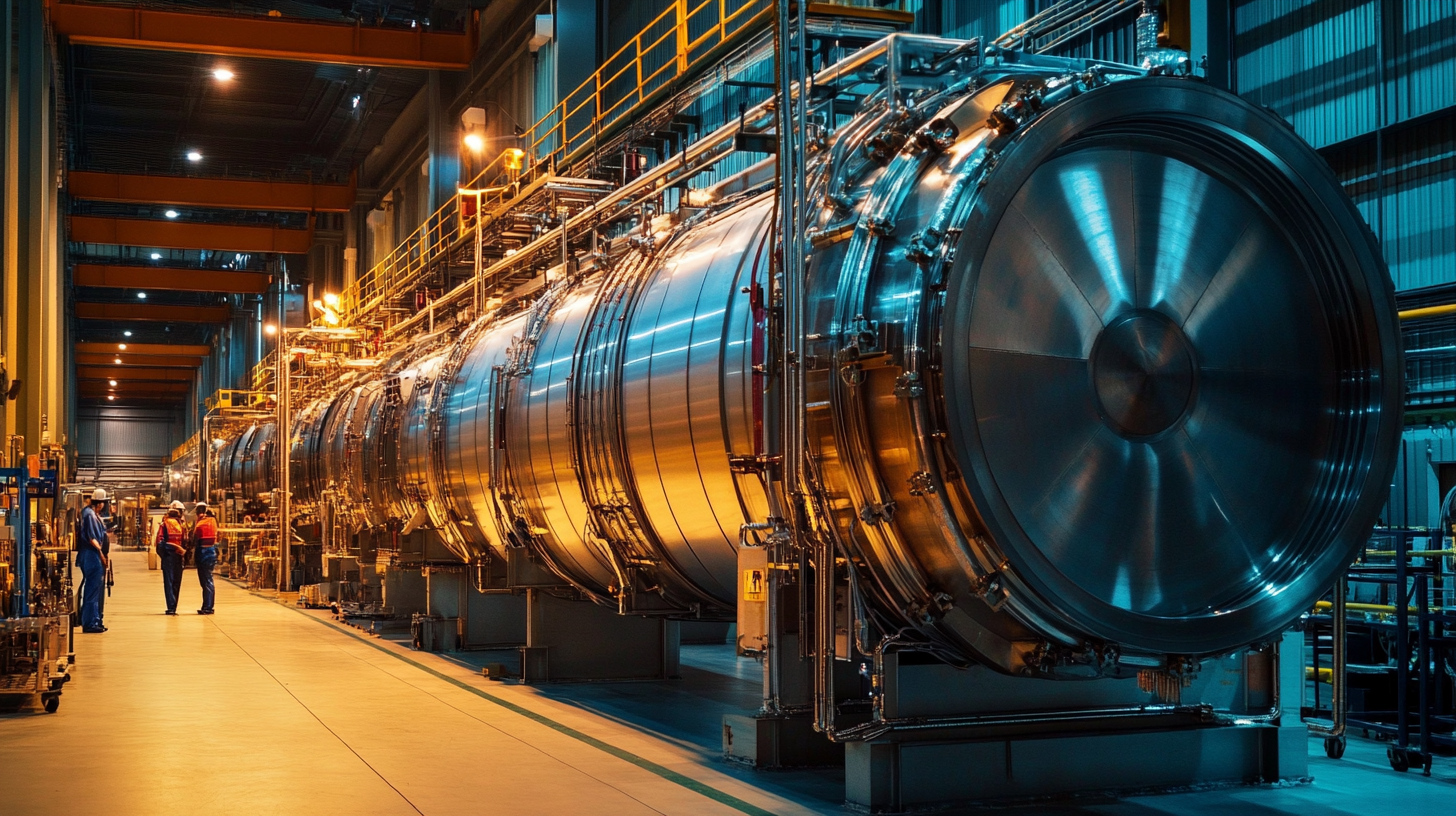
The Role of Automation in Optimizing Plasma Cutting Operations
The advent of automation in plasma cutting operations has revolutionized the manufacturing landscape, paving the way for enhanced efficiency and precision. As industries increasingly adopt advanced technologies, integrating automation systems into plasma cutting processes allows for reduced manual labor and minimized errors. Automated plasma cutting machines can work tirelessly, maintaining consistent quality while significantly increasing production speed. This shift not only optimizes throughput but also allows operators to focus on more strategic tasks, enhancing overall workplace productivity.
Incorporating automation also facilitates real-time monitoring and data analytics, which are critical for optimizing cutting parameters. By analyzing performance metrics, companies can make informed adjustments to improve material utilization and reduce waste. Automation systems can be equipped with predictive maintenance features, helping to anticipate equipment failures before they occur, thus minimizing downtime. As a result, manufacturers are able to maintain continuous operation, driving higher profitability while delivering superior products to the market.
Moreover, the integration of automation in plasma cutting processes fosters a safer working environment. By reducing the amount of manual intervention required, the risk of accidents decreases significantly. Automated systems can be designed to manage hazardous tasks, protecting employees and ensuring adherence to safety protocols. As the plasma cutting services market evolves, embracing these best practices will be crucial for businesses aiming to stay competitive and maximize their operational efficiencies in 2025 and beyond.
Sustainability Considerations in Plasma Cutting Services
The plasma cutting services market is undergoing significant transformations, especially with the growing emphasis on sustainability. As businesses strive to meet environmental regulations and consumer demands for greener practices, the integration of sustainable considerations into plasma cutting services has never been more critical. This transition not only aligns companies with modern environmental standards but also fosters innovation in operational processes.
Incorporating eco-friendly practices into plasma cutting involves using energy-efficient machinery and optimizing existing processes to reduce waste. Companies can invest in advanced plasma cutting technologies that minimize energy consumption while enhancing cutting precision. Additionally, utilizing recyclable materials and efficient waste management strategies can significantly lessen the ecological footprint of plasma cutting operations. Emphasizing sustainability can also lead to cost savings, proving that greener choices can benefit both the environment and the bottom line.
Furthermore, educating employees about sustainable practices is essential for maximizing efficiency. By fostering a culture of sustainability within teams, businesses can improve worker engagement and drive innovative ideas that contribute to more efficient operations. As the market moves towards 2025, organizations that prioritize sustainability in their plasma cutting services will not only comply with regulations but will also position themselves as leaders in an increasingly competitive and environmentally-conscious landscape.