Innovations in CNC Plasma Cutting: Transforming Industries in 2025 and Its Advantages
As we look toward the future of manufacturing, the advancements in CNC plasma cutting technology are set to revolutionize various industries by 2025. This innovative approach not only enhances precision in cutting complex materials but also significantly increases production efficiency. By harnessing the power of CNC (Computer Numerical Control) systems combined with plasma cutting techniques, businesses can achieve unparalleled accuracy in their projects. The ability to automate processes leads to a reduction in labor costs and a decrease in waste, fostering a more sustainable manufacturing environment.
The advantages of CNC plasma cutting extend far beyond mere cost savings. This technology empowers companies to tackle intricate designs and larger scale productions with ease, ultimately aligning with the growing demand for customized solutions. As industries continuously strive for improvement, the integration of CNC plasma cutting systems proves to be an essential step towards achieving operational excellence. With the potential to transform how various sectors, from automotive to aerospace, approach metal fabrication, the future of CNC plasma is bright and full of possibilities.
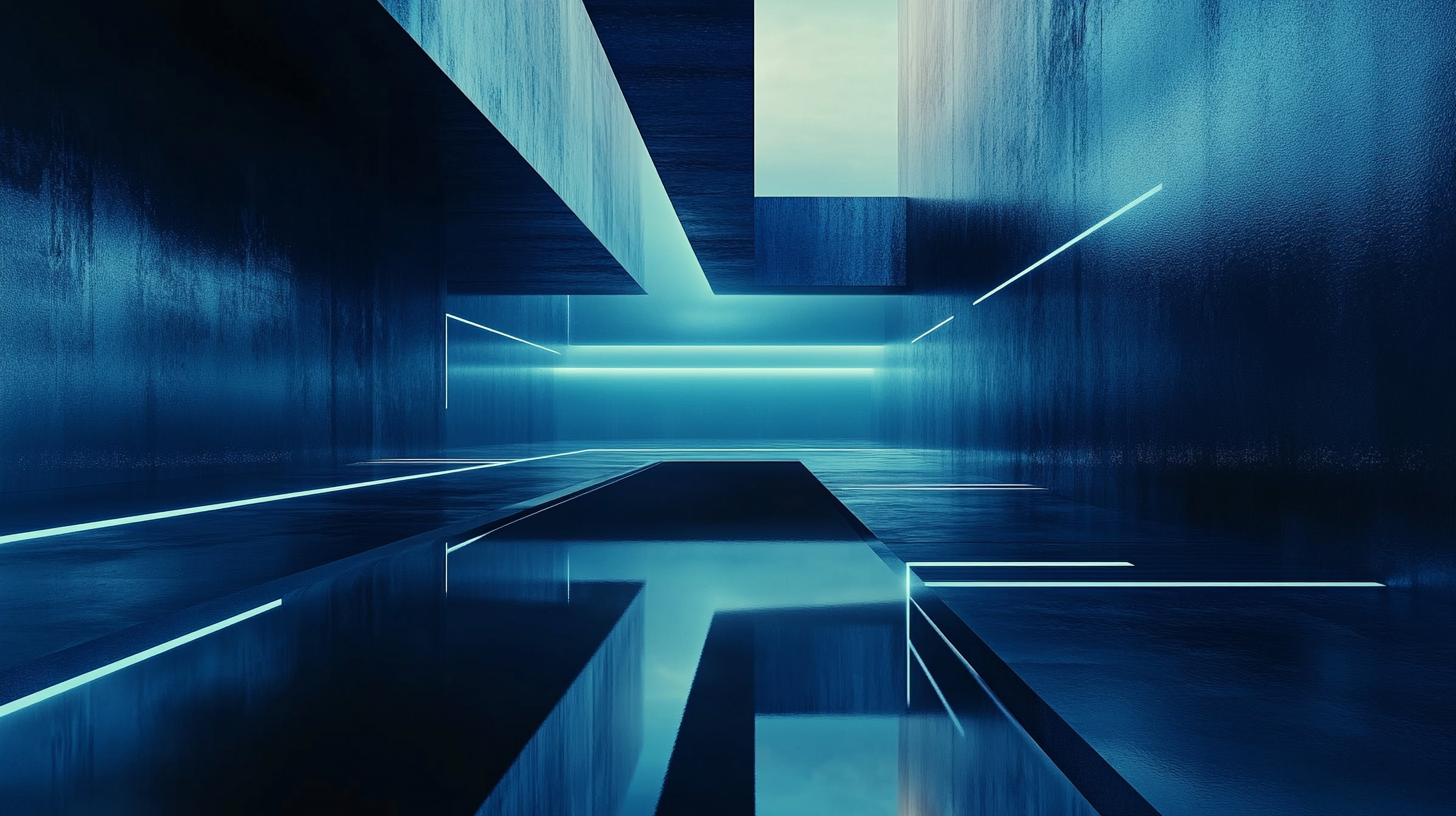
The Evolution of CNC Plasma Cutting Technology: What to Expect in 2025
As we look ahead to 2025, the CNC plasma cutting technology is set to undergo significant transformations that promise to reshape various industries. The evolution of this technology is intertwined with advancements in AI and high-precision machining, creating a new landscape for manufacturing processes. Expect an increase in demand for CNC plasma cutting machines, with market projections indicating a growth of over 5.1% from 2025 to 2034. This growth is largely driven by the need for versatile and efficient cutting solutions across sectors ranging from automotive to aerospace. China's rapid ascent as a leader in advanced manufacturing directly impacts the innovation trajectory of CNC plasma cutting technologies. With substantial investments in research and development coupled with the capabilities of domestic companies, we can anticipate groundbreaking advancements that will enhance cutting precision and efficiency. Companies like ProArc are at the forefront, continuously pushing the envelope in high-performance cutting solutions, which will likely be reflected in the broader market. The integration of smart technologies and multi-axis machining centers is another critical aspect of this evolution. As industries seek to reduce waste and improve productivity, CNC plasma cutting machines equipped with artificial intelligence will facilitate more adaptive and intelligent manufacturing systems. This shift not only enhances operational efficiency but also aligns with the global push for sustainable manufacturing practices. As we move closer to 2025, the landscape of CNC plasma cutting is poised for remarkable growth, driven by innovation and the relentless pursuit of excellence in manufacturing.
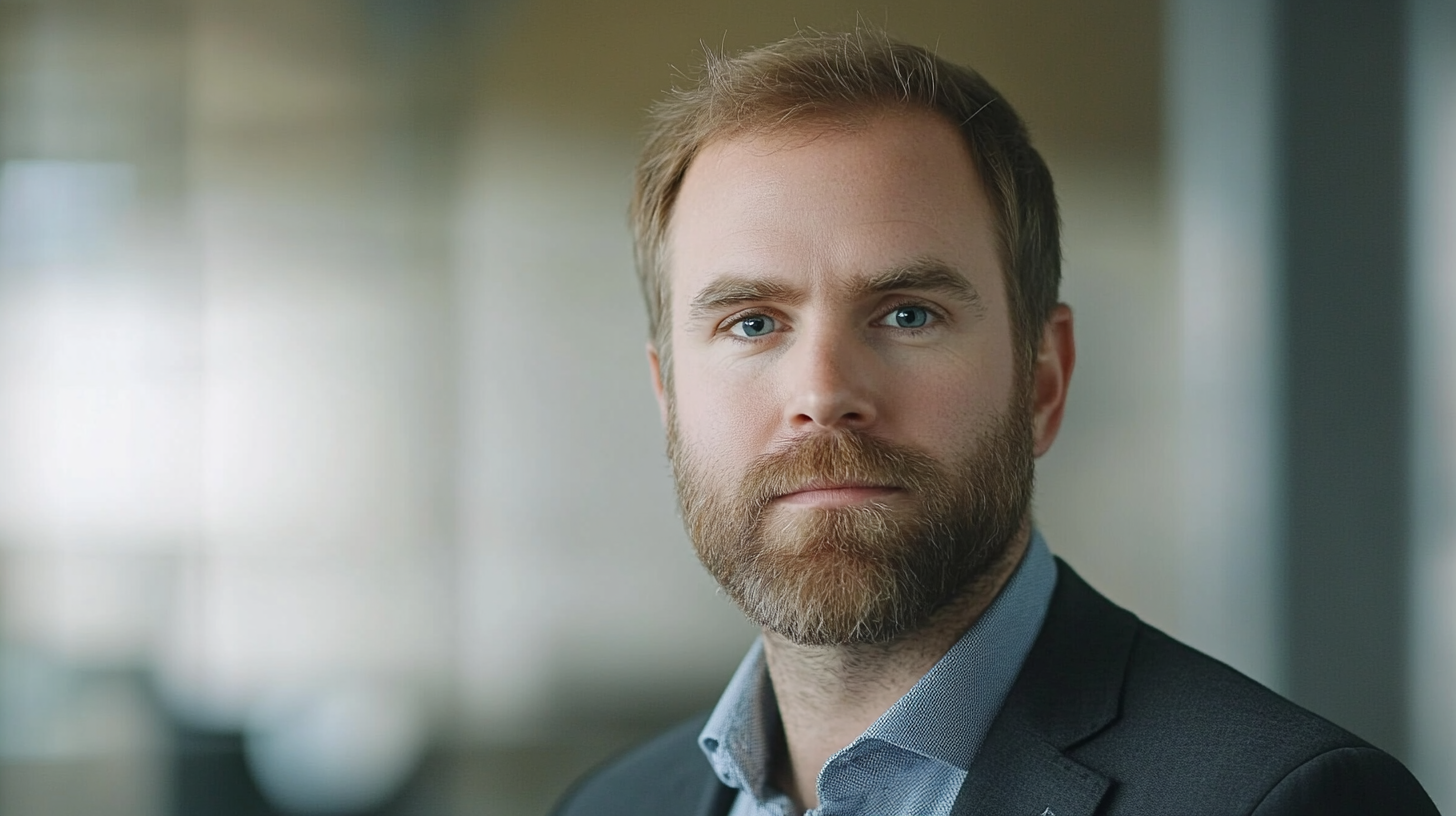
Key Innovations Driving Efficiency and Precision in Plasma Cutting
In 2025, the CNC plasma cutting industry is set to experience unprecedented growth driven by key innovations that dramatically enhance efficiency and precision. According to a report by MarketsandMarkets, the global plasma cutting market is projected to reach USD 5.47 billion by 2026, growing at a CAGR of 5.2%. This growth is fueled by advancements in cutting technology and automation, which are transforming how industries operate.
One of the most significant innovations is the integration of Artificial Intelligence (AI) in CNC systems. AI algorithms can analyze cutting patterns, optimize parameters in real-time, and reduce material waste by up to 20%. Moreover, advancements in software applications enable manufacturers to develop more complex designs while maintaining higher tolerances, leading to improvements in productivity levels, which can increase output by as much as 30%.
Additionally, the introduction of high-definition plasma cutting has revolutionized the precision of the process. High-definition plasma technology allows for sharper cuts and cleaner edges, reducing the need for secondary finishing processes. A study from Research and Markets highlights that companies adopting this technology have reported up to 50% savings in production costs. The increasing automation of CNC plasma cutting systems also significantly reduces manual intervention, further ensuring consistency and accuracy in the production line.
With these innovations, industries relying on plasma cutting—from automotive to aerospace—are not only improving their production capabilities but also enhancing overall quality control. The benefits of increased efficiency, reduced costs, and higher precision position CNC plasma cutting as a crucial technology in the competitive landscape of manufacturing in 2025.
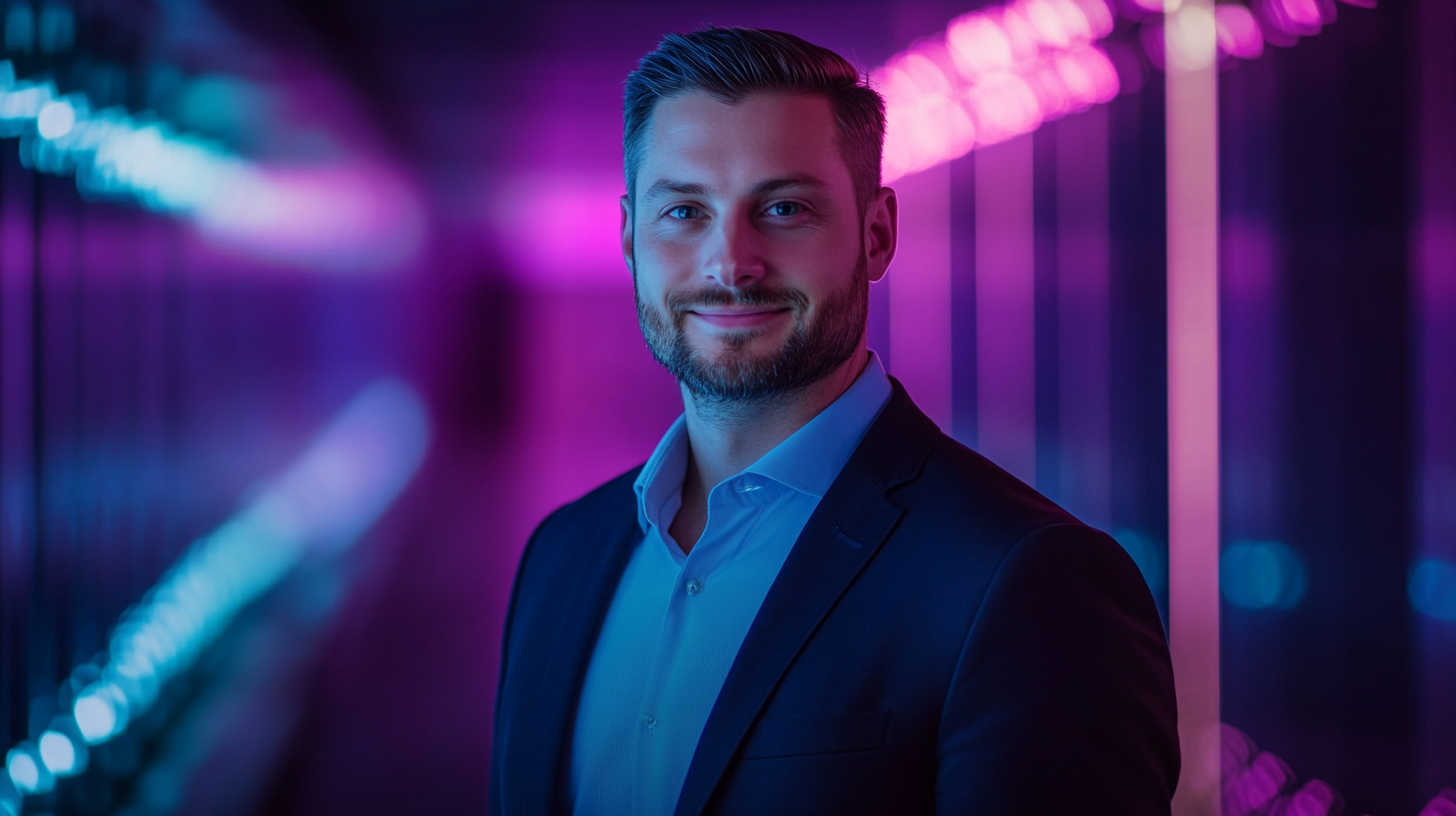
Impact of Advanced Software Solutions on CNC Plasma Cutting Techniques
The landscape of CNC plasma cutting is undergoing a significant transformation, driven primarily by advanced software solutions that are revolutionizing techniques in the manufacturing sector. These innovations harness powerful algorithms and machine learning to enhance precision, efficiency, and adaptability in cutting processes. By leveraging real-time data and feedback, industries can see remarkable improvements in their operational workflows, ultimately leading to higher quality outputs and reduced waste.
Moreover, as the market for plasma cutting machines continues to expand—with a projected growth reflected in the surge of digital cutting technologies—companies are investing heavily in these advanced software applications. The integration of artificial intelligence and automation in CNC plasma cutting allows for dynamic adjustments during the cutting process, enabling machines to operate not only with greater accuracy but also with increased safety features. This paradigm shift is particularly evident in sectors like garment manufacturing, where efficiency and precision are crucial, as businesses pioneer advancements in both cutting and sewing techniques.
Additionally, regions known for their manufacturing prowess are rapidly embracing these technological advancements. With countries like China leading the way in innovation, the competitive landscape is evolving. The proliferation of next-gen CNC machining technologies is set to reshape not just individual companies but whole industries, making the synergy between advanced software solutions and CNC plasma cutting a focal point for the future. This technological revolution is not just about cutting metal; it's about cutting through inefficiencies and unlocking new possibilities for production.
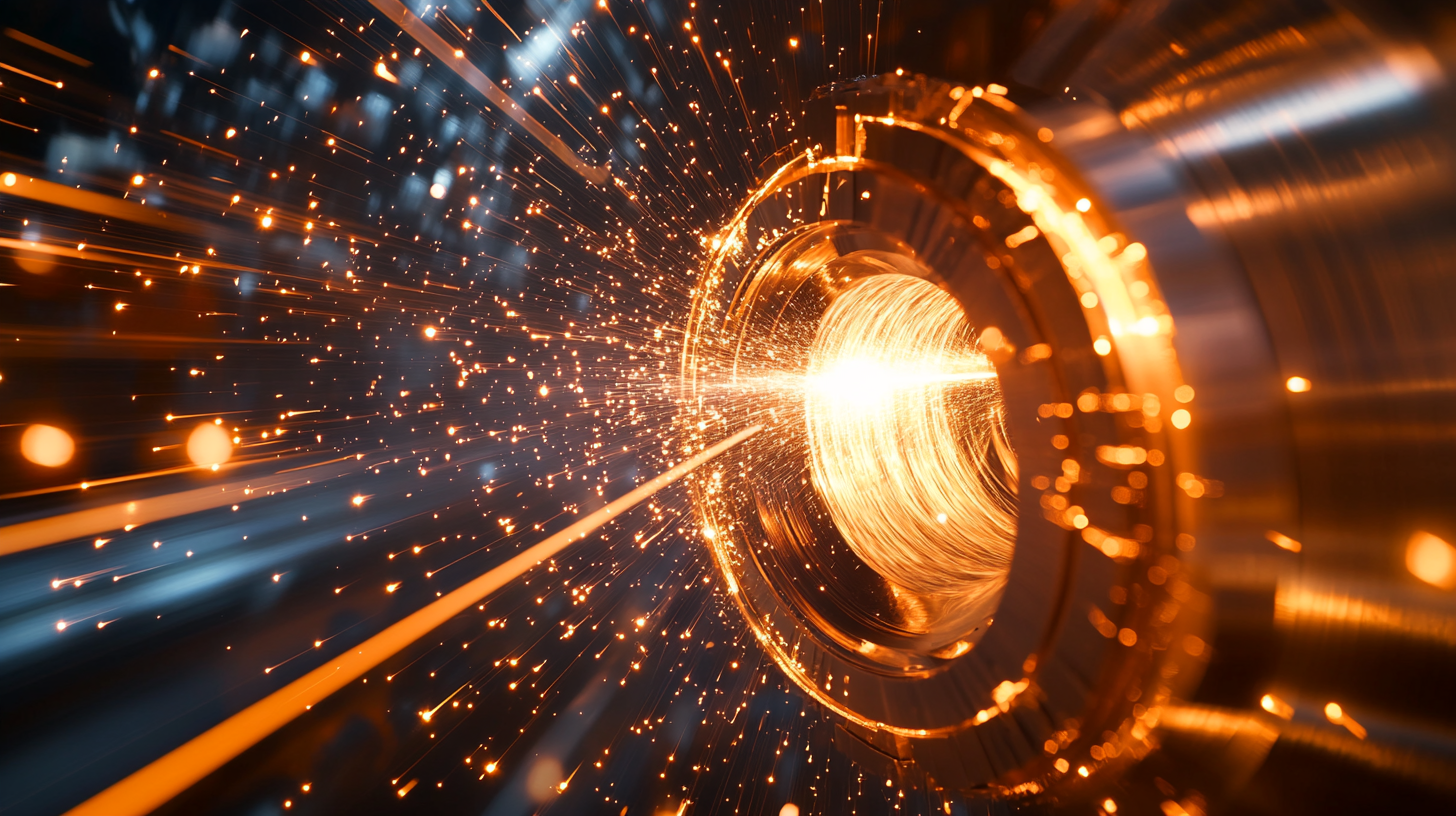
Comparative Benefits of CNC Plasma Cutting Over Traditional Methods
CNC plasma cutting technology has emerged as a game-changer in various industries, driving efficiency and precision beyond what traditional cutting methods can achieve. One of the most significant advantages of CNC plasma cutting is its speed. Compared to traditional cutting techniques, which often involve slower processes, CNC plasma cutting can deliver intricate designs and cuts rapidly, drastically reducing production timelines. This speed not only enhances productivity but also allows businesses to respond quickly to market demands.
Another key benefit is the accuracy that CNC plasma cutting provides. Designed to work in conjunction with computer numerical control, this technology enables manufacturers to achieve highly precise cuts with minimal kerf width. Traditional methods, such as oxy-fuel cutting, often lead to broader cuts and more material wastage. Precision is vital in industries such as aerospace and automotive, where even the slightest deviation can impact overall performance and safety. Thus, CNC plasma cutting ensures a higher level of quality control and material efficiency.
Furthermore, the adaptability of CNC plasma cutting technology stands in stark contrast to traditional methods that may require significant reconfiguration for different projects. CNC systems can be easily programmed to switch between different materials and thicknesses, making them ideal for versatile production environments. This flexibility not only optimizes workflow but also allows manufacturers to explore innovative designs without the constraints typically associated with conventional cutting processes.
Future Trends: Sustainable Practices in CNC Plasma Cutting Industries
As industries continue to evolve, CNC plasma cutting is increasingly incorporating sustainable practices that not only enhance efficiency but also minimize environmental impact. According to a report by Market Research Future, the global CNC plasma cutting machine market is expected to grow at a CAGR of 5.8% from 2021 to 2028, highlighting a shift towards technologies that prioritize sustainability alongside performance. This transition is largely driven by regulatory pressures and the growing demand for eco-friendly manufacturing processes.
One significant trend in CNC plasma cutting is the integration of energy-efficient technologies. Modern plasma cutting machines are now designed to consume less energy while maintaining high cutting speeds and precision. Research indicates that adopting energy-efficient systems can reduce operational costs by up to 30%, making them not only beneficial for the environment but also economically advantageous for manufacturers. Furthermore, the use of recycled materials in conjunction with advanced CNC plasma cutting techniques is gaining traction, leading to reduced waste and a smaller carbon footprint for production facilities.
Another notable sustainable practice is the implementation of water-cooled plasma systems, which minimize airborne pollutants and enhance safety in the working environment. According to the Fabricators & Manufacturers Association, transitioning to such systems can decrease harmful emissions by as much as 40%. This aligns with global initiatives aiming for more sustainable manufacturing standards, showcasing how technological advancements in CNC plasma cutting not only elevate productivity but also foster a responsible approach to industrial operations.