Global Manufacturing Guidelines for Cnc Plasma Cutting Machine Innovations
In the ever-evolving landscape of manufacturing, the integration of advanced technologies such as the CNC plasma cutting machine has revolutionized production processes across various industries. These machines, known for their precision and efficiency, play a crucial role in metal fabrication and other cutting applications. As businesses strive to enhance their operational efficacy, understanding the global manufacturing guidelines surrounding these innovations becomes imperative. This blog will delve into the essential standards and best practices that govern the use of CNC plasma cutting machines, ensuring that manufacturers can optimize their resources and achieve superior results.
Moreover, the adoption of CNC plasma cutting technology not only boosts productivity but also supports sustainability efforts by minimizing waste and energy consumption. With increasing competition and the need for high-quality output, manufacturers must stay informed about upcoming trends and innovations. By exploring the global manufacturing guidelines that accompany these machines, we aim to equip industry professionals with valuable insights that foster growth, enhance safety, and promote environmental responsibility in the manufacturing realm. Join us as we navigate through the vital aspects of CNC plasma cutting machine innovations and their implications for the future of manufacturing.
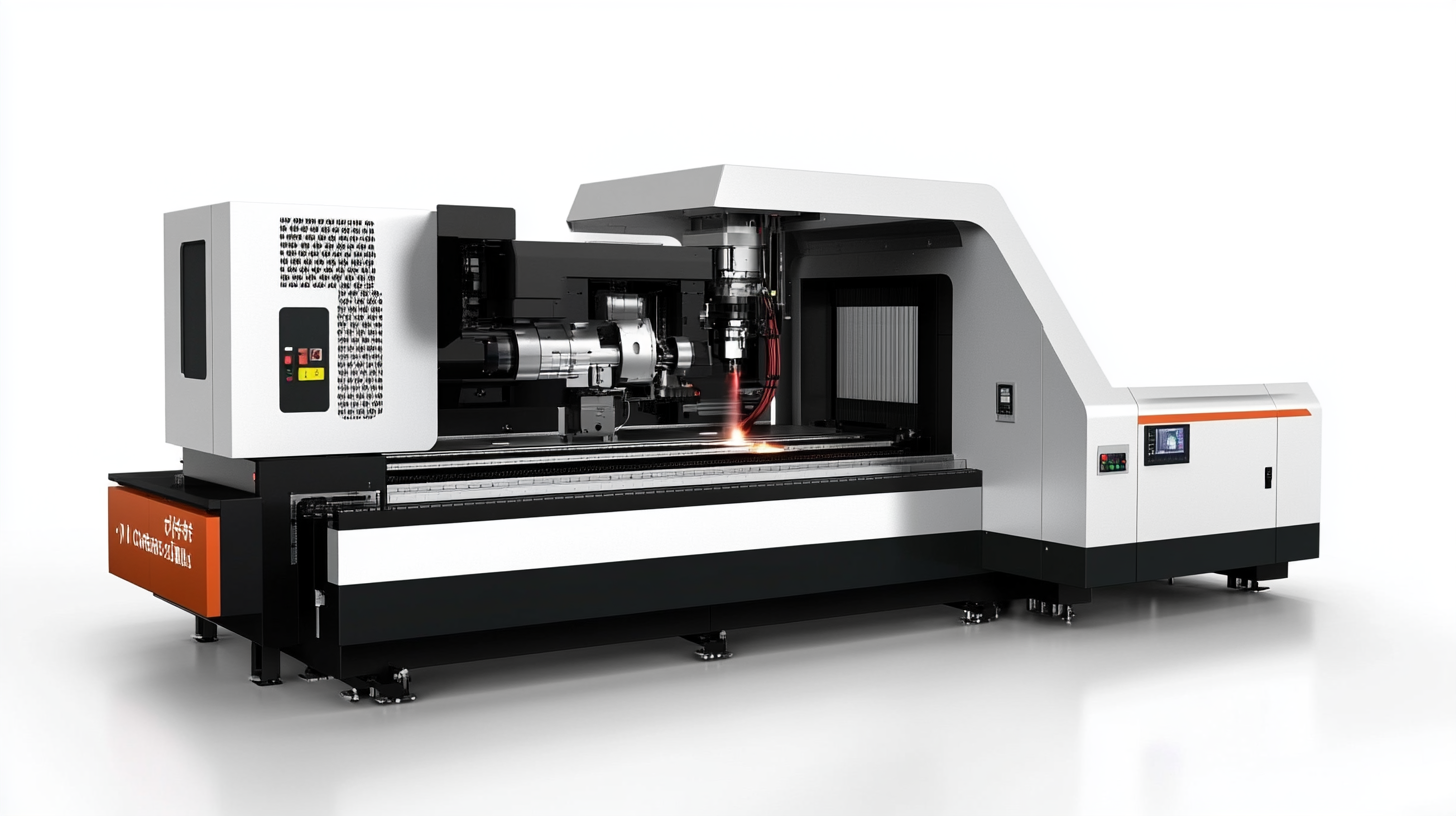
Innovative Technologies Shaping the Future of CNC Plasma Cutting Machines
In recent years, the landscape of CNC plasma cutting machines has undergone significant transformation, driven by innovative technologies that are reshaping possibilities in the manufacturing sector. One notable advancement is the integration of AI and machine learning algorithms into plasma cutting systems. These enhancements allow for real-time adjustments during the cutting process, improving accuracy and reducing material waste. By leveraging data analytics, manufacturers can now optimize cutting paths and minimize downtime, ultimately leading to increased productivity and efficiency. Another exciting development is the incorporation of advanced software solutions that provide intuitive user interfaces and enhanced control features. Users can easily design complex cuts with precision, adapting to various materials and thicknesses seamlessly. This level of customization not only boosts creative potential for designers but also simplifies the setup process, making CNC plasma cutting more accessible to a wider range of users. Moreover, the rise of IoT (Internet of Things) technology facilitates remote monitoring and maintenance of CNC plasma cutting machines. Operators can receive real-time updates and diagnostics directly from their machines, enabling proactive maintenance and reducing the likelihood of unexpected failures. This seamless connectivity fosters a more responsive production environment, allowing businesses to maintain a competitive edge in a rapidly evolving market. As these innovative technologies continue to shape the future of CNC plasma cutting machines, manufacturers are poised to reap the benefits of enhanced efficiency, precision, and creativity, paving the way for a new era in manufacturing capabilities.
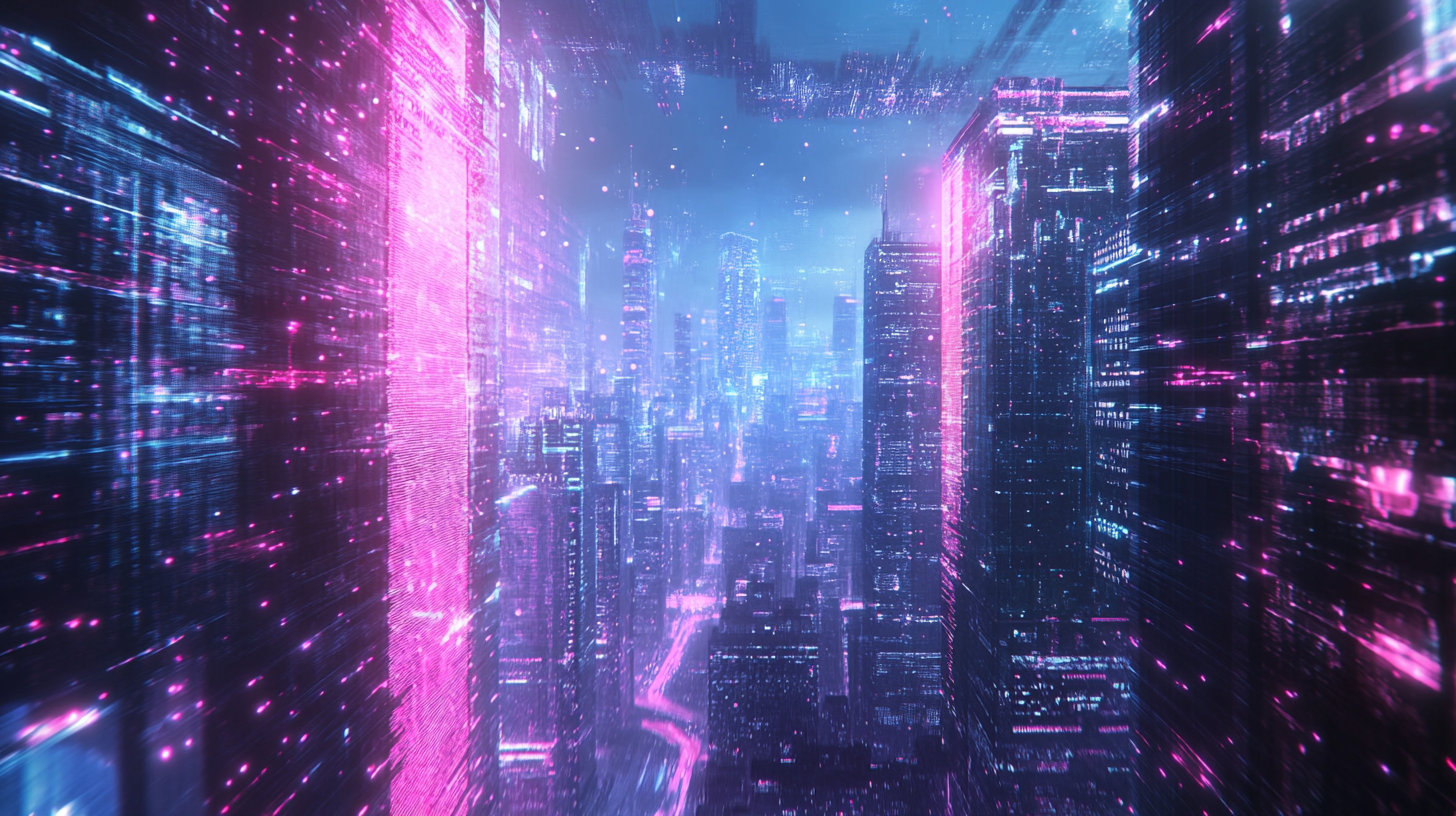
Key Global Trends in CNC Plasma Cutting Machine Manufacturing
The CNC plasma cutting machine market is witnessing dynamic growth, driven by the increasing demand for precision and efficiency in manufacturing processes. In 2023, the market size stands at $646.2 million and is projected to reach $841.4 million by 2030, growing at a compound annual growth rate (CAGR) of 3.8%. This growth is indicative of a broader trend in smart manufacturing, where technology transformation is reshaping production efficiencies and capabilities.
Key global trends influencing CNC plasma cutting machine manufacturing include the rise of automation and the integration of advanced technologies. The increasing adoption of CNC (computer numerical control) systems enables manufacturers to achieve higher accuracy and reduced wastage, thereby enhancing overall productivity. Furthermore, the aerospace and automotive industries are significantly contributing to market expansion, with a growing preference for CNC plasma cutting machines due to their versatility and ability to handle complex applications.
Additionally, manufacturers are focusing on innovation regarding power sources, such as the shift from conventional to inverter technologies, which offer better energy efficiency and performance. As these trends continue to evolve, the focus on sustainability and cost-effectiveness will further drive advancements in CNC plasma cutting technology, positioning it as a cornerstone in the future of global manufacturing.
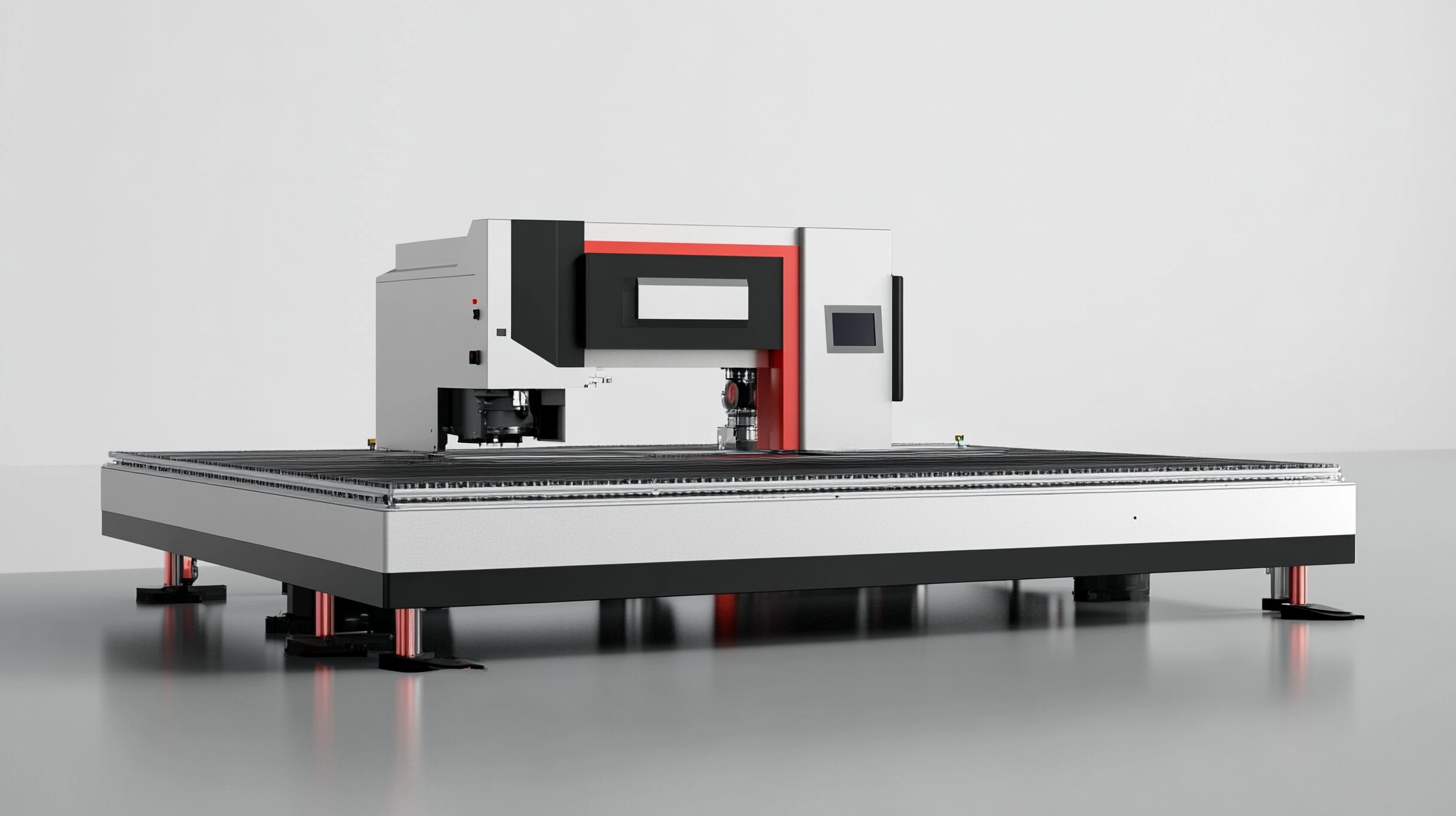
Best Practices for Enhancing Efficiency in Plasma Cutting Processes
In the evolving landscape of manufacturing, enhancing efficiency in plasma cutting processes is paramount for industries aiming to stay competitive. The growing significance of using nickel-based alloys in plasma cutting, due to their superior mechanical properties, particularly emphasizes the need for optimized cutting parameters. Innovative practices in plasma arc cutting can significantly reduce waste and production time, resulting in a marked improvement in overall operational efficiency.
Recent advancements in plasma-driven processes highlight a new era for manufacturing, particularly in niche applications such as additive manufacturing at the atomic scale. By integrating these advanced methodologies, manufacturers can refine their production processes, leading to greater efficiency and lower operational costs. Utilizing techniques that minimize downtime during plasma cutting operations, such as quick-change setups and effective nesting strategies, can further enhance material utilization and productivity.
Data reports underline that modern innovations can potentially reinvigorate industrial manufacturing, which has faced declining productivity levels. For example, implementing plasma-activated processes for various applications can facilitate decentralized production strategies, thus overcoming traditional limitations. By focusing on adopting emerging technologies and best practices, manufacturers can achieve significant performance improvements in their plasma cutting operations, paving the way for more sustainable and efficient production methods.
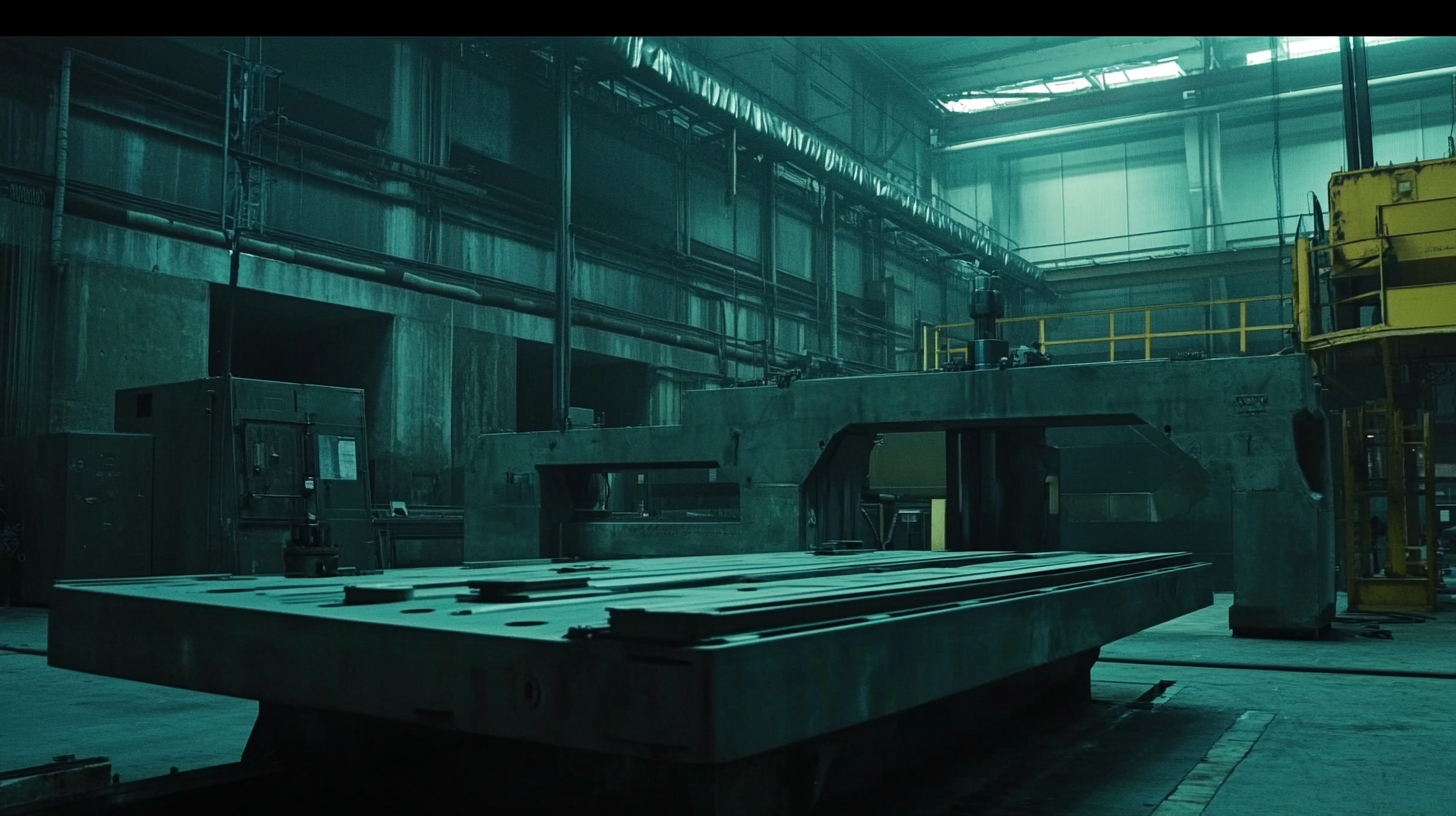
Sustainable Manufacturing Strategies for CNC Plasma Cutting Innovations
In the ever-evolving landscape of manufacturing, sustainable strategies are becoming paramount, especially concerning CNC plasma cutting innovations. The integration of green supply chain management (GSCM) practices plays a critical role in enhancing the performance of manufacturing firms. By prioritizing eco-friendly processes, companies can minimize waste, optimize resource use, and ultimately improve their bottom line. This shift not only addresses ecological concerns but also aligns with the growing consumer demand for sustainable products.
Furthermore, innovations in technologies such as the new electrical pulse method for carbon fiber recycling exemplify how manufacturers can adopt sustainable practices. This transformative approach not only reduces material wastage but also enhances the lifecycle management of key materials used in CNC plasma cutting machines. Embracing such advancements positions companies to lead in both operational efficiency and environmental stewardship.
In addition, the emergence of partnerships, such as those between India and CSIRO, highlights the importance of collaborative efforts in pushing forward sustainable innovations. By pooling resources and expertise, industries can tackle the multifaceted challenges of sustainability more effectively. As global manufacturers increasingly recognize the socio-cultural and environmental implications of their operations, the pathway to greener innovations in CNC plasma cutting becomes clearer and more attainable.
The Impact of Automation on CNC Plasma Cutting Machine Development
The landscape of CNC plasma cutting machines is undergoing a transformative shift, primarily fueled by advancements in automation. As industries seek to enhance efficiency and productivity, the integration of automated systems into the operation of CNC plasma cutting machines has become essential. This technological progression not only streamlines manufacturing processes but also minimizes human error, leading to higher precision in cutting and shaping metal components.
Automation in CNC plasma cutting embodies a convergence of sophisticated software, robotics, and machine learning algorithms. This synergy allows manufacturers to achieve greater plasma productivity by optimizing cutting paths, adjusting parameters in real-time, and ensuring consistent quality across production runs. The ability to automate routine tasks frees up skilled operators, enabling them to focus on more complex processes that demand critical human oversight.
Moreover, the impact of automation transcends mere efficiency gains. It enables companies to respond swiftly to market demands and adapt to innovations in material science and cutting technologies. As the global manufacturing landscape evolves, those adopting automated CNC plasma cutting solutions will likely position themselves at the forefront of modernization, ready to meet the challenges of an increasingly competitive marketplace.