Unlocking Precision Cutting with the Best Cnc Plasma Table Specifications and Usage Guide
In the ever-evolving landscape of manufacturing and fabrication, precision cutting has become a cornerstone of efficiency and accuracy. Among the various tools available, the **Best CNC Plasma Table** stands out as a revolutionary equipment that combines technology with artistry. Its ability to deliver intricate and precise cuts on a wide variety of materials makes it an indispensable asset for professionals and DIY enthusiasts alike. This blog aims to explore the essential specifications of the best CNC plasma tables and provide a comprehensive usage guide, ensuring that you can maximize the capabilities of this groundbreaking tool.
Understanding the specifications of the best CNC plasma table is crucial for anyone looking to enhance their cutting projects. From the power settings to the size of the cutting area, each feature plays a vital role in determining the effectiveness of your work. By delving into the nuances of these tables, you can make informed decisions that cater to your specific needs, whether you are operating in a small workshop or a large-scale manufacturing environment. Join us as we unlock the potential of CNC plasma cutting and guide you toward achieving precision and excellence in your projects.
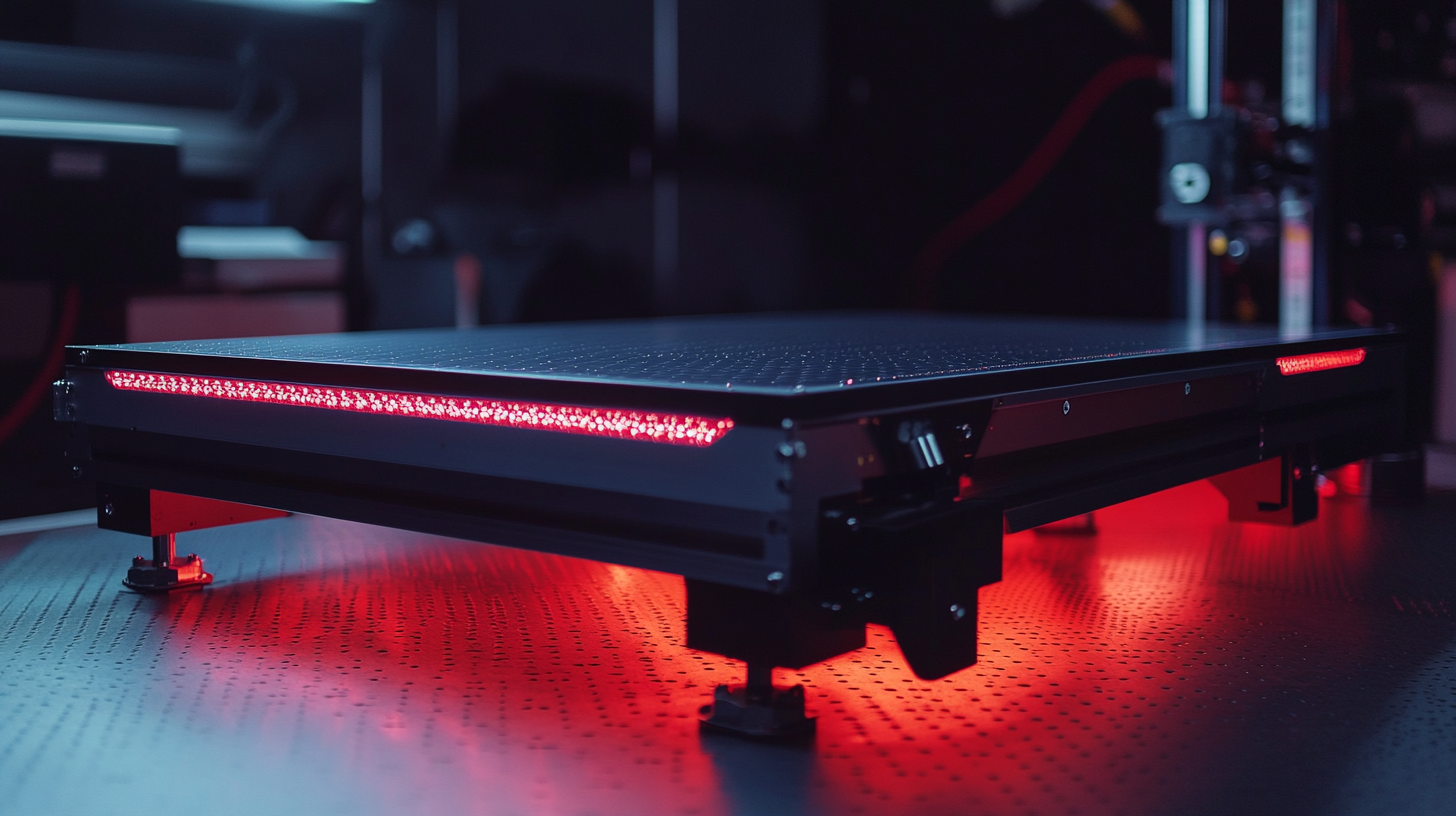
Understanding CNC Plasma Cutting Technology for Optimal Results
CNC plasma cutting technology has revolutionized the manufacturing industry, providing a high level of precision and efficiency. By utilizing computer numerical control, operators can conduct intricate cuts in various materials with minimal human intervention. This technology not only enhances the quality of cuts but also significantly reduces production time. Understanding the specifics of CNC plasma tables, including their specifications and intended use, is essential for achieving optimal results in any fabrication process. Recent advancements have emphasized the integration of ultrasonic sensors in CNC plasma cutting systems. Research conducted by institutions such as Fraunhofer IGCV and the University of Augsburg highlights how these sensors can correlate sound patterns with the quality of composite material processing. By analyzing the acoustics of the cutting process, manufacturers can gain insights into the effectiveness of their setups, allowing for real-time adjustments and improved outcomes. This fusion of technology ensures that precision remains at the forefront, making it possible to achieve consistent high-quality results across various projects. As the industry continues to evolve, leveraging tools like ultrasonic measurement in conjunction with advanced CNC plasma tables can provide a competitive edge. Emphasizing a deeper understanding of the cutting process will not only enhance individual projects but can also lead to significant advancements in material engineering and overall manufacturing efficiency. Exploring the latest technologies in CNC plasma cutting assures that operators are well-equipped to meet the demands of modern fabrication.
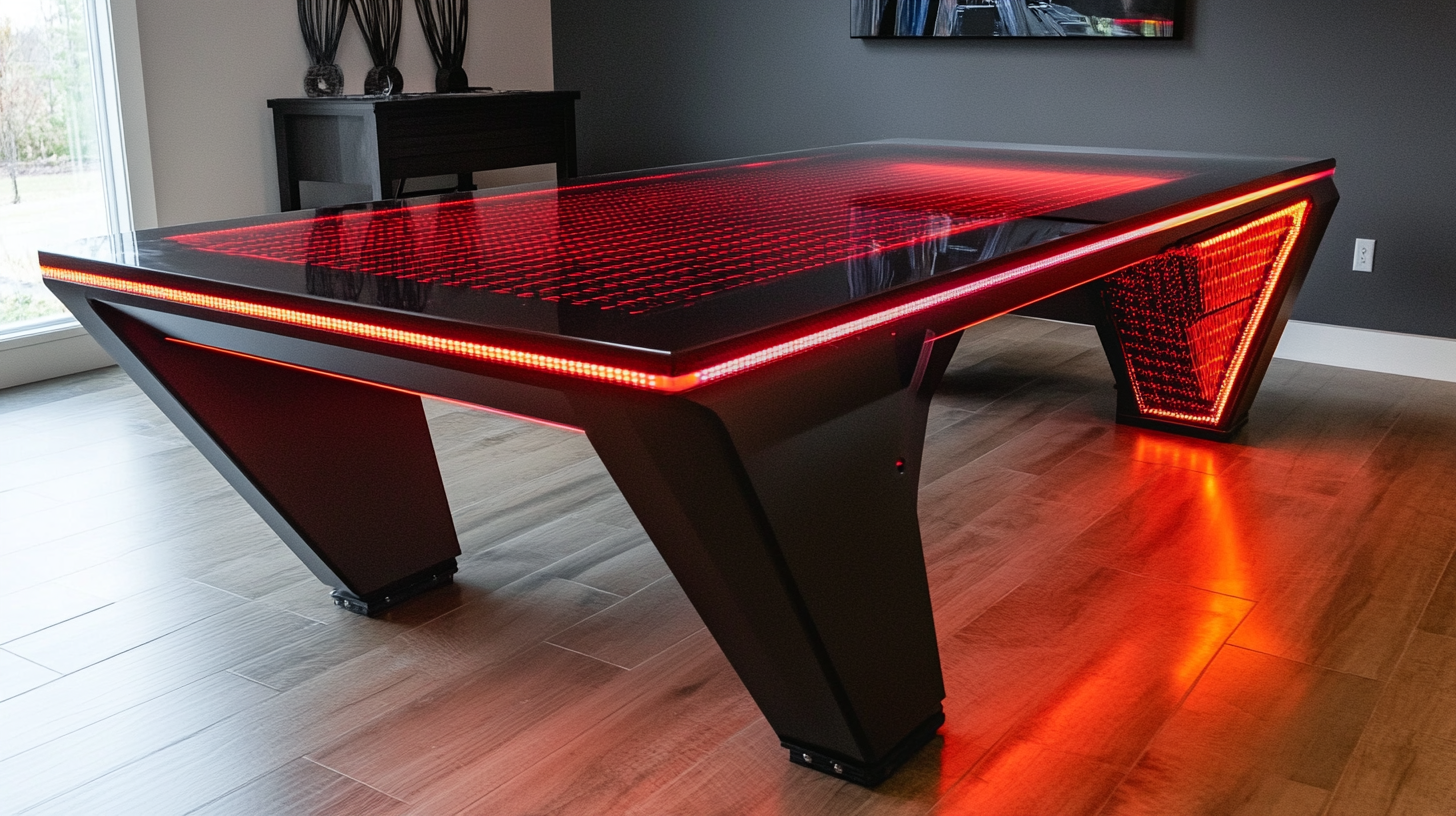
Key Specifications to Consider When Choosing a CNC Plasma Table
When selecting a CNC plasma table, several key specifications significantly influence performance and versatility. First and foremost, bed size plays a crucial role. A larger table provides ample space for bigger projects, allowing for more extensive cutting patterns and reducing the need for repeated setups. It’s essential to consider both the maximum sheet size and the effective work area, as these determine what materials and projects can be effectively handled.
Another critical specification is the cutting thickness capacity. Different plasma tables offer varying cutting capabilities, which is important depending on the materials you intend to work with. If your projects involve thicker metals, ensure that the CNC plasma table is equipped with a high-performance plasma cutter that supports-depth cutting. This specification will prevent operational limitations and enhance overall productivity.
Additionally, the type of motion system, whether it be gantry-style or table-style, impacts precision and speed. The gantry systems are often favored for their stability and higher speed, which can lead to more efficient operations. Coupled with a reliable software package that supports advanced features such as CNC programming and design integration, these specifications can greatly enhance the user's experience and the quality of the finished product. Selecting the right combination of these features will ensure that your CNC plasma table meets your specific needs, delivering precision and efficiency in every cut.
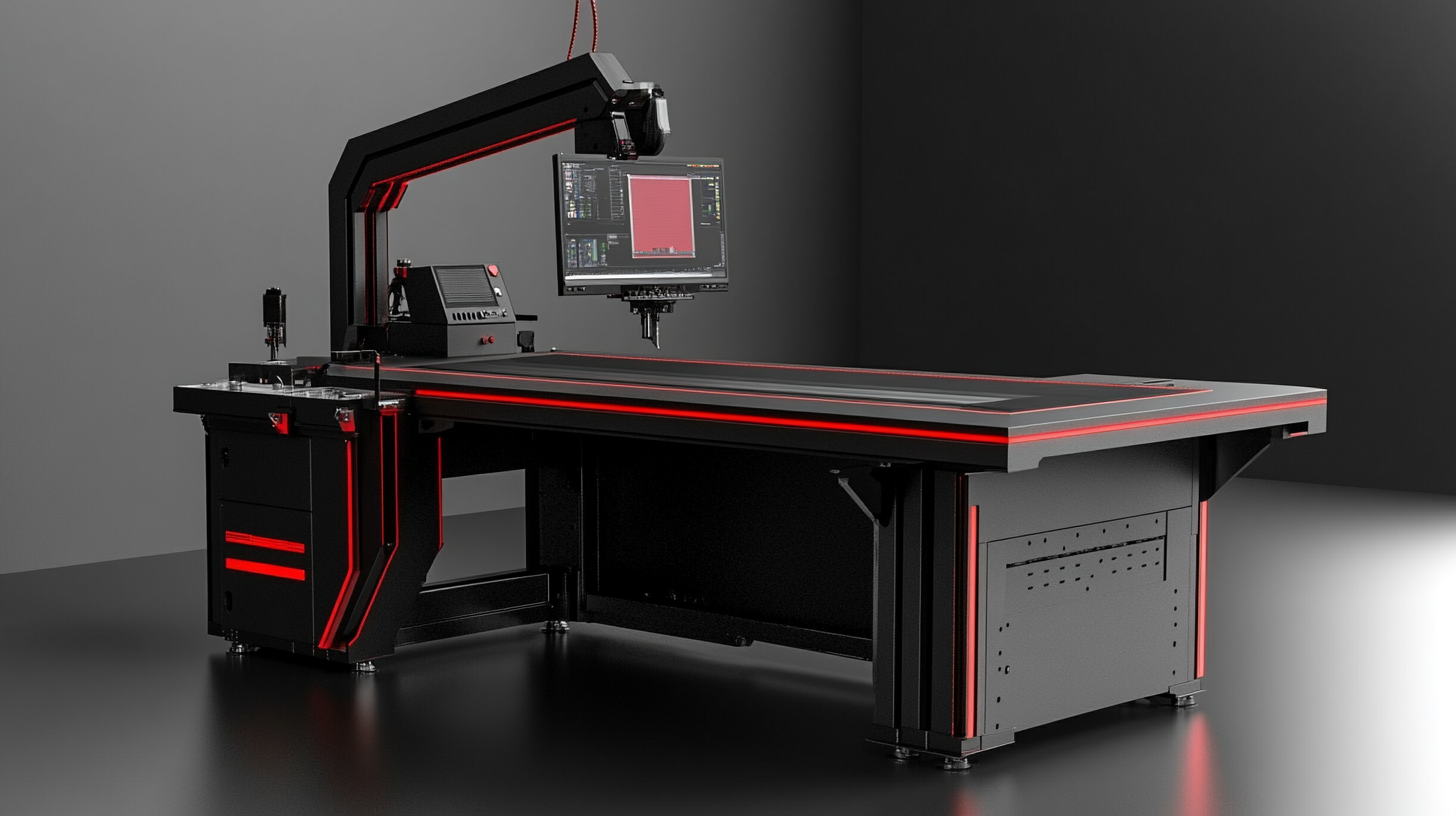
Essential Features of a High-Performance CNC Plasma Table
When it comes to investing in a CNC plasma table, understanding the essential features that contribute to high performance is crucial for both amateur and professional metalworkers. Key specifications that should be prioritized include cutting speed, precision, and the ability to handle various materials. A high-performance CNC plasma table should feature advanced software that allows for intuitive design and seamless integration with CAD programs. This enhances accuracy and efficiency, enabling users to achieve intricate designs easily.
Another standout feature is the power source of the plasma cutter. A reliable and adjustable plasma power source allows users to modify the cut settings according to material thickness and type, reducing the likelihood of burn-through and enhancing the overall quality of the cut. Proper cooling systems should also be included to maintain optimal operation and extend the lifespan of the equipment.
Moreover, the physical build of the CNC plasma table plays a significant role in its performance. A sturdy frame and adjustable legs ensure stability, which is critical during the cutting process. Additional features like an integrated water table can help manage smoke and debris, improving the workspace while also prolonging the life of consumables. Together, these elements form the backbone of an effective CNC plasma table, ready to tackle diverse projects with precision and reliability.

Tips for Effective Usage and Maintenance of Your CNC Plasma Table
In the world of metalworking, precision and efficiency are paramount, especially when utilizing CNC plasma tables. Effective usage and maintenance of these cutting-edge tools can significantly impact output quality and operational cost. For example, studies reveal that when properly calibrated, CNC plasma cutters can achieve a cutting speed of up to 100 inches per minute, with a thermal cut tolerance as tight as ±0.05 inches, demonstrating how critical specification adherence is for optimal performance.
Regular maintenance of CNC plasma tables is essential for sustaining their high efficiency and longevity. Industry reports indicate that a significant percentage of operational downtime—up to 30%—can result from inadequate maintenance practices. Basic upkeep routines, such as checking consumable wear and ensuring the proper alignment of the cutting head, not only enhance performance but also extend the lifespan of the machinery. Additionally, maintaining a clean work surface and regularly inspecting electrical connections can prevent costly repairs and unplanned interruptions in production.
Moreover, utilizing the right specifications tailored to specific tasks can vastly improve operational effectiveness. For instance, plasma tables equipped with advanced control systems can allow for greater flexibility in design and material handling, with some models supporting sheet sizes up to 5’ x 10’. This adaptability proves invaluable for shops looking to maximize their capabilities without significant investment in multiple machines or technologies. Thus, understanding the nuances of CNC plasma table specifications and implementing rigorous maintenance protocols can unlock unparalleled precision and efficiency in metalworking endeavors.
Common Applications and Benefits of CNC Plasma Cutting in Industry
CNC plasma cutting technology is revolutionizing various industries by providing high precision and efficiency in metal fabrication. One of the most notable advantages of CNC plasma cutting is its ability to produce intricate designs with minimal waste. This is particularly beneficial in sectors such as automotive, aerospace, and metalworking, where precision and detail are paramount. The technology allows for quick setup and modification, enabling manufacturers to adapt to changing designs and production needs without significant downtime.
At the recent Laser World of Photonics Exhibition in Germany, advancements in laser technology were showcased, indicating a future where cutting technologies will increasingly integrate innovative solutions. Just as CNC plasma cutting has enhanced traditional metalworking, the developments in industrial femtosecond lasers demonstrate potential for next-generation applications. These laser advancements promise improved cutting capabilities that could complement or even surpass those of plasma cutting, particularly in regard to the precision and quality of the finished product.
The common applications of CNC plasma cutting range from creating components for machinery and equipment to artistic metal structures. With its ability to cut through various materials like steel, aluminum, and copper, the CNC plasma table is becoming an essential tool across diverse sectors. As industries evolve and adopt more sophisticated technologies, the integration of CNC plasma cutting continues to provide a competitive edge while opening up new possibilities for innovation in material processing.