Unlock Precision and Efficiency in Manufacturing with Our Advanced Cnc Cutters
In today’s competitive manufacturing landscape, companies are consistently seeking ways to enhance precision and efficiency in their production processes. One groundbreaking solution that has gained prominence is the CNC cutter, a tool that has revolutionized the way we approach machining tasks. With its ability to automate intricate cutting processes, the CNC cutter minimizes human error, accelerates production rates, and allows for consistent delivery of high-quality results. As industries evolve, the adoption of advanced CNC cutting technology becomes not only an advantage but a necessity for manufacturers aiming to stay ahead of the curve.
Investing in state-of-the-art CNC cutters equips businesses with the tools to optimize their operations and achieve unparalleled precision. These machines are engineered to handle a diverse range of materials and complexities, making them indispensable in various sectors from aerospace to automotive manufacturing. In this blog, we will explore how incorporating advanced CNC cutters can unlock new levels of efficiency and reliability, ultimately transforming your manufacturing processes and positioning your business for sustained success.
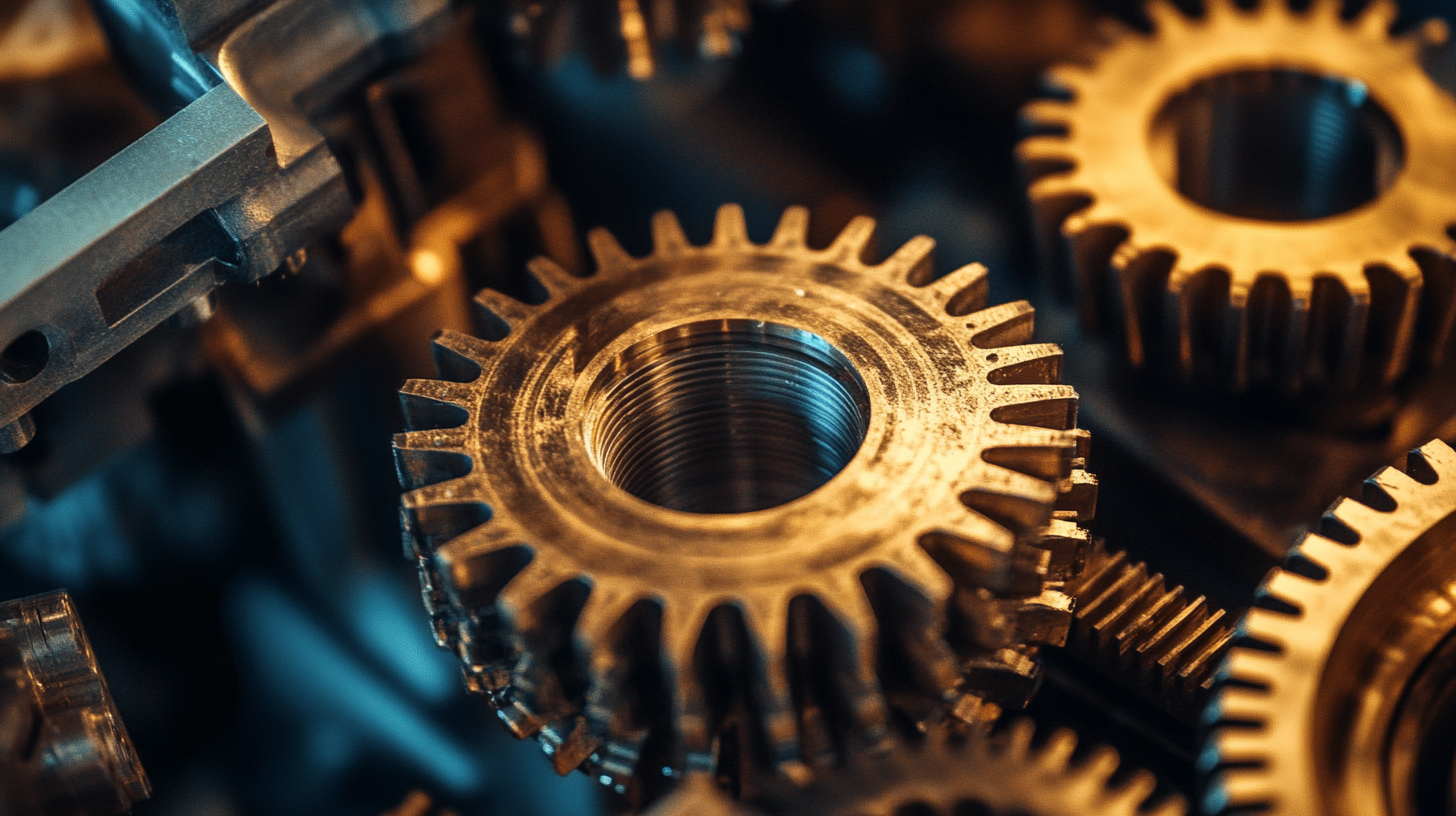
Revolutionizing Manufacturing: The Role of CNC Cutters in Precision Engineering
In today's rapidly evolving manufacturing landscape, the role of CNC (Computer Numerical Control) cutters has become increasingly pivotal in revolutionizing precision engineering. These advanced tools facilitate unparalleled accuracy and efficiency, making them indispensable for manufacturers seeking to stay competitive in an ever-demanding market. The integration of AI technology with CNC machining not only enhances the precision of cuts but also streamlines operations, ensuring that manufacturers can reduce costs while accelerating production times. As industries recognize the importance of high-precision manufacturing, the demand for innovative CNC solutions continues to soar. This trend is particularly evident in sectors like medical device manufacturing, where the ability to produce intricate, high-quality components rapidly is critical. The combination of subtractive and additive manufacturing technologies is transforming the landscape, enabling quicker time-to-market and fostering improvements in healthcare through enhanced device reliability and performance. Moreover, the CNC machine tools market is on the brink of significant growth, driven by the rising need for multi-axis machining centers. This evolution highlights a shift towards sophisticated manufacturing techniques that embrace both precision and efficiency. As we look ahead, it’s clear that CNC cutters will play a vital role in shaping the future of manufacturing, propelling industries towards new heights of innovation and excellence.
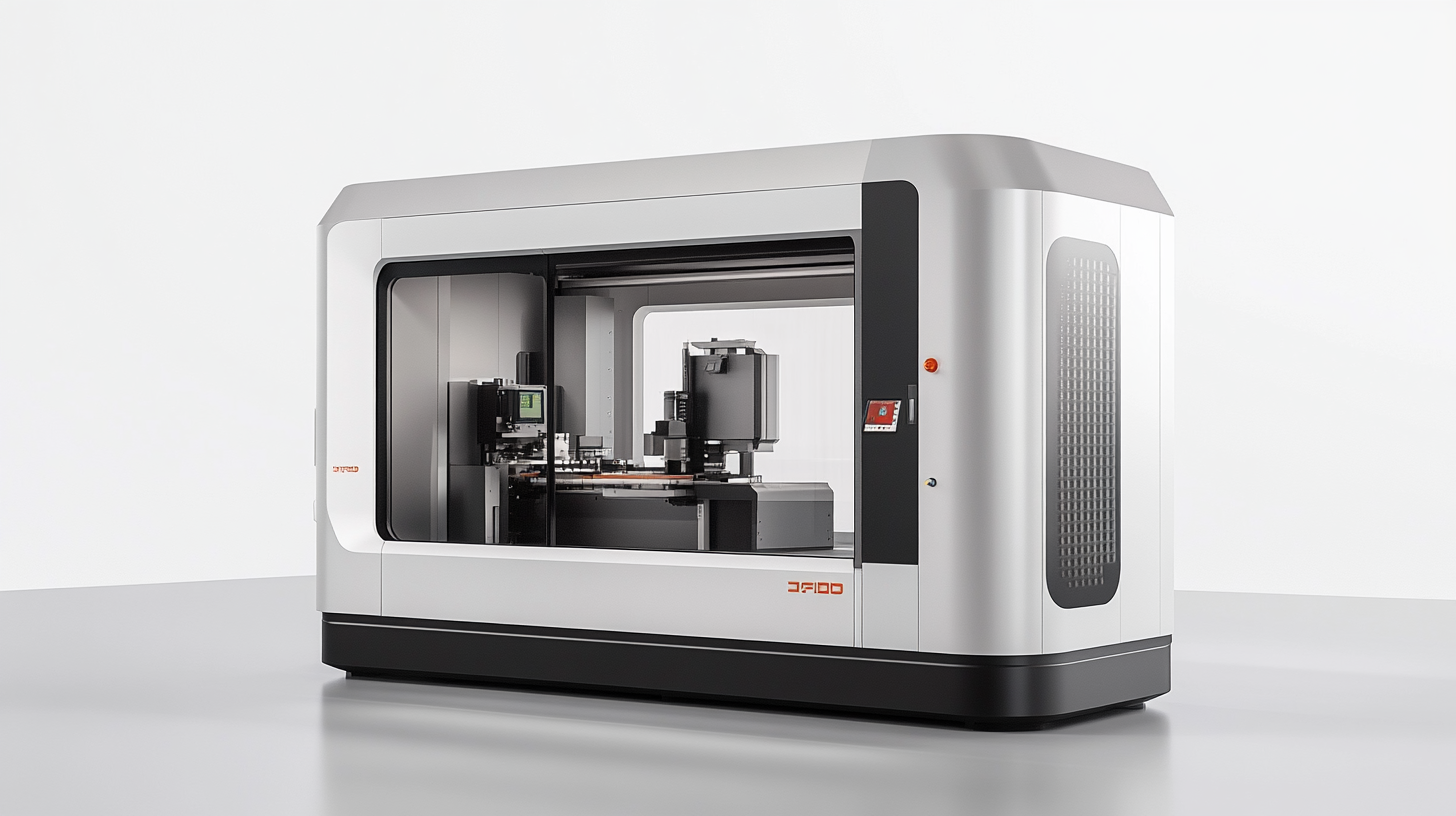
Enhancing Efficiency: How Advanced CNC Cutters Reduce Production Time
The manufacturing industry is on the cusp of a significant transformation, driven by the increased demand for precision and automation. According to recent research by SNS Insider, the market size for advanced CNC machines is projected to reach a staggering US$ 162.16 billion by 2032. This growth is largely fueled by the efficiency gains that CNC technology offers, allowing manufacturers to reduce production times and enhance overall output.
Advanced CNC cutters are at the heart of this revolution, enabling businesses to streamline processes and minimize waste. By integrating artificial intelligence into CNC operations, companies are unlocking new levels of productivity, optimizing machining processes, and reducing cycle times. The demand for automation in manufacturing is not merely a trend; it is a necessary evolution in response to the pressures of global competition and the need for higher precision in production.
Furthermore, specialized applications like CNC fabric cutting have redefined production capabilities in the textile industry. These advanced machines deliver faster cutting speeds and greater accuracy compared to traditional methods, ensuring that manufacturers can meet the evolving demands of the market swiftly. As the industry continues to embrace these emerging technologies, the anticipated annual growth rate of 6.5% for the laser cutting machines market from 2025 to 2034 indicates a robust future for precision-driven manufacturing solutions.
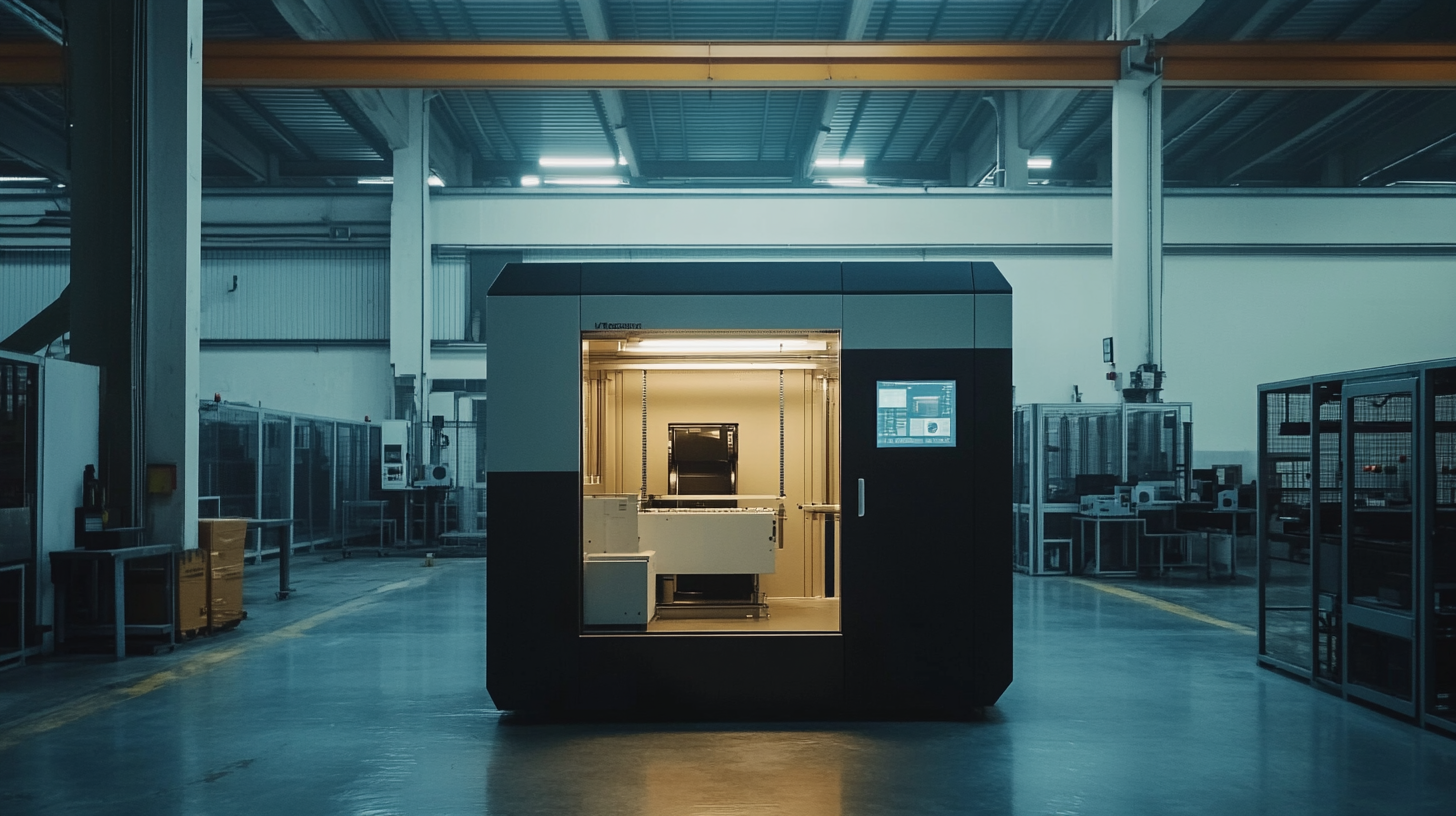
Maximizing Material Utilization: Cost Savings with Modern CNC Technology
In the ever-evolving landscape of manufacturing, maximizing material utilization has become a cornerstone for cost savings and operational efficiency. Modern CNC technology offers remarkable solutions for cutting down on waste, transforming the way materials are handled in production. One of the most effective strategies for achieving this is through automatic nesting software. This advanced technology optimizes the layout of cuts on fabric or sheet material, ensuring that every inch is utilized wisely. By minimizing leftover scraps, manufacturers can significantly reduce material costs and enhance their overall sustainability.
CNC fabric cutting has emerged as a game changer in textile manufacturing, allowing for precise cuts that traditional methods struggle to match. The integration of CNC technology streamlines the cutting process, reduces labor costs, and increases throughput. The precision of CNC machines ensures that each piece adheres to exact specifications with minimal errors, leading to less rework and waste. Additionally, the flexibility of CNC fabric cutting allows manufacturers to adapt quickly to changing orders or designs without impacting the quality or efficiency of production.
Meanwhile, advancements in laser cutting technology continue to reshape metal fabrication. By adopting the latest laser cutting techniques, metal fabricators are able to enhance their capabilities, achieving intricate designs and superior edge quality. As equipment continues to improve, the return on investment in cutting technology becomes apparent, as manufacturers can take on a wider range of projects while keeping costs in check. Overall, these innovations in cutting technology not only improve material utilization but also pave the way for a more efficient and cost-effective manufacturing process.
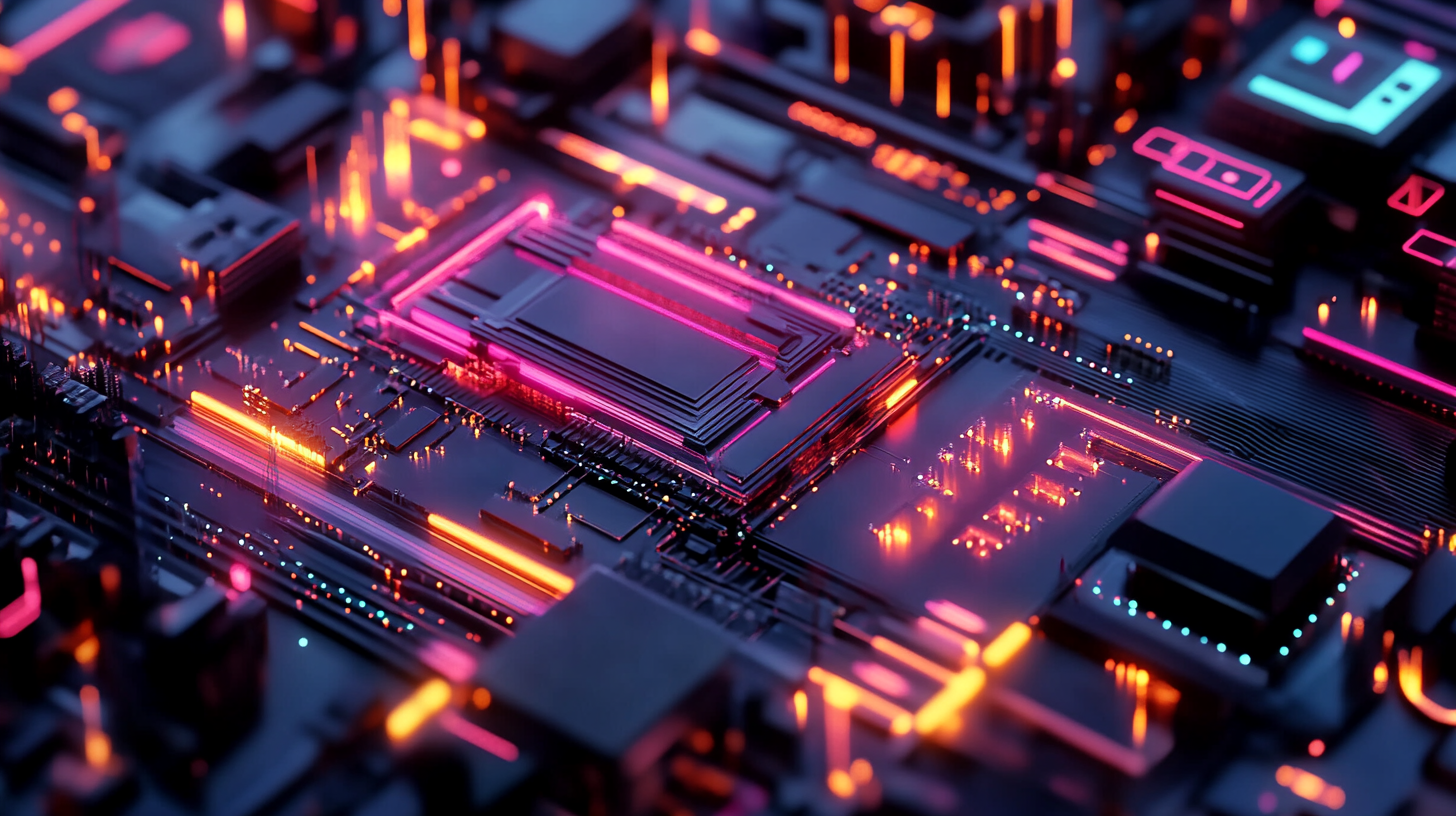
The Future of Manufacturing: Innovations in CNC Cutter Design and Functionality
In the rapidly evolving landscape of manufacturing, the innovations in CNC cutter design and functionality are paramount. As industries across the globe embrace advanced manufacturing technologies, CNC cutters are leading the charge by enhancing precision and efficiency. Recent reports indicate that the global CNC machine market is projected to reach USD 100 billion by 2025, underscoring the vital role these tools play in modern manufacturing.
With an emphasis on developing new productive forces, regions like Hubei are revitalizing traditional industries while simultaneously fostering new ones. This dual approach not only underscores the necessity of state-of-the-art equipment but also highlights the importance of innovations like intelligent CNC systems. These systems facilitate higher accuracy and reduce waste, ultimately leading to more sustainable manufacturing practices. As evidenced by leading companies in the field, continuous investment in advanced machinery significantly boosts productivity and quality.
Moreover, participation in international exhibitions, such as the recent China International Machine Tool Exhibition, showcases the industry's commitment to embracing cutting-edge technologies. Manufacturers are increasingly focusing on the integration of smart technologies with traditional CNC machining, paving the way for a future where automation and human expertise coexist harmoniously. The trajectory is clear: the future of manufacturing hinges on innovations that not only improve productivity but also align with broader strategic goals such as sustainability and economic resilience.
Integrating CNC Cutters into Your Workflow: Best Practices for Manufacturers
Integrating CNC cutters into manufacturing workflows can drastically improve productivity and precision. According to a report by Market Research Future, the global CNC machine market is projected to grow at a CAGR (Compound Annual Growth Rate) of 6.5% between 2020 and 2026, highlighting the increasing reliance on advanced machining technologies. By adopting CNC cutters, manufacturers not only enhance efficiency but also achieve higher levels of repeatability in their production processes.
One best practice for integrating CNC cutters is to invest in comprehensive training for operators. A study conducted by the Association for Manufacturing Technology (AMT) found that companies that prioritize workforce training can see efficiency improvements of up to 35%. Ensuring that operators are well-versed in both the machinery and software will lead to optimized machining strategies, minimizing errors and maximizing output quality.
Another key consideration is the importance of maintaining an optimal machine layout. According to Lean Manufacturing principles, strategically placing CNC cutters within the workflow can reduce unnecessary movement and downtime. Implementing a cellular manufacturing layout can lead to a 25% increase in productivity, as it allows for faster changeovers and improved workflow integration. By focusing on these best practices, manufacturers can unlock the full potential of CNC technology, positioning themselves for sustained growth in a competitive market.